Being an electrician can be dangerous! 97% of electricians have been either shocked or injured on the job.
And that’s not all.
There are 30,000 incidents of electric shock hazards recorded annually. Over 1,000 electricians die every year in fatal electrical accidents.
Worst of all, medical expenses for severe electrical burns can easily exceed $4 million per person.
What does this all mean?
It is essential to always be mindful of electrical safety concerns and take necessary precautions.
As an electrician, you may already know that safety is of the utmost importance. But even with all your experience and knowledge, there are probably some things about electrical safety that you are unaware of or often overlook.
This article will provide 11 fascinating and little-known facts about electrical safety tips. We hope you find them helpful!
11 Electrical safety tips you should follow at all times
Electrical safety is a top priority for electricians. The right precautions can prevent serious injuries and deaths, so make sure you take these 11 steps when working on a residential or commercial electrical project.
1. Deenergize systems before performing any work
OSHA’s electrical standards always stress de-energizing electrical circuits before electricians start working on them. There are only three exceptions to this rule: life-support equipment, emergency alarm systems, and hazardous area ventilation equipment.
In all other cases, electrical outlets and circuits over 50 volts need to be de-energized and the device must be placed in an electrically-safe work condition before an electrician performs any work. NFPA 70E lists six steps that must be followed to ensure an electrically safe work condition:
- Determining all possible electrical supply sources by looking at blueprints, diagrams, and ID tags
- Disconnect every available source of electrical power by interrupting the load current using appropriate measures
- Double check whether all blades of disconnected devices are fully open and draw-out-type circuit breakers are disconnected completely
- Apply proper lockout/tagout procedures for all devices and equipment as per the documented or established policies
- Use a voltage detector to check whether the electrical circuit and phase conductors are de-energized
- If there is a chance of induced voltages or stored electrical energy, use ground fault circuit interrupters to de-energize them
2. Follow proper lockout/tagout (LOTO) protocols
The lockout/tagout procedures in electrical work are very crucial to the safety and well-being of people working on site. A proper lockout/tagout (LOTO) procedure must cover these eight steps outlined by OSHA.
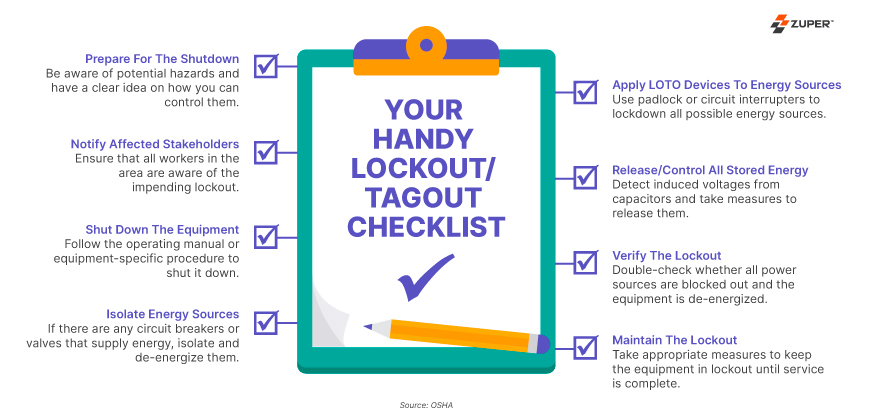
Proper lockout/tagout procedures ensure that electrical circuits do not re-energize and cause potential harm to people in contact. According to OSHA, every place with industrial machinery requires a proper lockout/tagout program, and all electricians must have the correct lockout tagout equipment.
3. Perform electrical hazard analysis on all circuits above 50 volts
Before electricians start working on an electrical circuit with an energy of 50 volts and higher, it is mandatory to perform a thorough electrical hazard analysis. The NFPA 70E article specifies that all types of electrical hazard analysis (Shock, Arc-Flash, Arc-Blash, and Burns) must be performed on the electrical circuit.
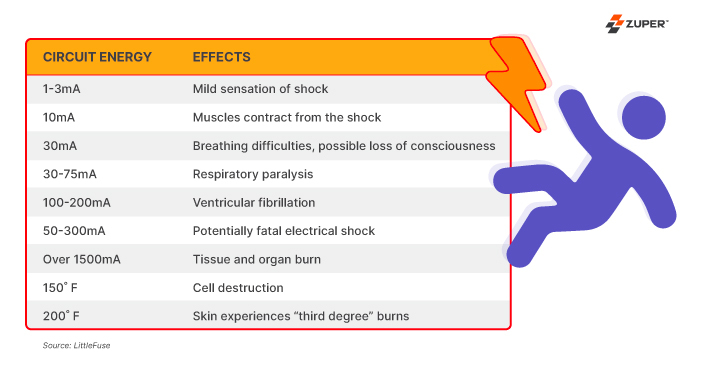
4. Apply appropriate warning labels to all equipment
Once the electrical hazard analysis is complete, electricians must make the effort to affix appropriate warning labels on equipment. This particular safety standard was added to NFPA 70E in the year 2000. Later on, around 2002, NEC came up with a standard to specify shock and Arc-Flash hazards with a clear warning label.
5. Get proper certification to work on energized equipment
In addition to being trained on the equipment, hazards, and electrical safety precautions, electricians need to get “qualified” to work on energized equipment. NFPA 70E clearly states that a detailed energized electrical work permit must be obtained by the electrician before he/she can work on energized equipment.
These permits help supervisors or managers (who are the signing authorities) to understand the additional risks involved in working on energized circuits. These work permits don’t merely ensure that the worker is qualified for the job but also shift the decision to work on energized equipment from the electrician to the management.
6. Prepare exhaustive job briefs and plans
When working on or near exposed, energized electrical conductors and circuit parts it is important to have a job briefing before electricians work on energized or near-exposed circuits or electrical equipment.
A proper briefing must include:
- A discussion on potential electrical hazards associated with the task
- Procedures or tasks that need to be completed during the job
- Special precautions that must be taken while working
- Instructions on where and how to remove the source of energy
- Details on emergency response and communication modes
- A list of required personal protective equipment (PPE)
7. Wear proper protective clothing
Appropriate personal protective equipment (PPE) must be selected based on specific tasks and hazard levels. While OSHA 1910.173 provides valuable information on the maintenance of PPE kits, NFPA 70 E offers a wealth of insights on selecting the right PPE kit for a job.
In order to meet OSHA and NFPA 70E guidelines, electricians must wear minimum flame retardant clothing, safety goggles, and protective gloves when they work on or approach an energized circuit. Protective insulating blankets or mats can be used to minimize the exposure further. NFPA standards state that PPE kits need to be repaired, cleaned, or washed as per the manufacturer’s instruction prior to every use. Also, PPE kits must be inspected thoroughly before and after a job.
8. Make sure there is adequate lighting
When electricians are working, they must ensure that there is adequate lighting to illuminate their work environment. Portable lights should be fully insulated so as not to accidentally cause short circuits when used near power lines or other equipment which may create electromagnetic fields.
9. Use protective barricades or barriers around hazards
The use of barriers during electrical work is key to preventing the injury of unqualified individuals. Barricades can be used for any type or size of job, and they warn children and adults living close to the potential hazard.
The cabinet doors of electrical panels should always be closed. The panels should never have holes; this helps prevent the exposure of live wires. If any electrical panel cannot be closed, there should be barriers, shields, or other insulating materials around it.
10. Be prepared for the unexpected
Electricians must not only be trained and knowledgeable about their line of work but also be familiar with emergency procedures. All electrical workers must be aware of emergency communication methods and have trained medical personnel ready when working on potentially hazardous electrical tasks.
Preparation is the key to ensuring electrical safety. Before an electrician works on a task, they should consider what could go wrong and plan accordingly. When they are prepared to face the worst, they can mitigate and overcome any challenge that is ahead of them.
11. Use protective devices wherever possible
Current-limiting devices reduce the potential for electrical hazards by limiting how much current can flow through them. Here are some benefits of using current-limiting overcurrent protective devices:
- They reduce the voltage on circuit boards thus eliminating the chance of short circuits
- They prolong device life by limiting the current level through parts that may be quickly heated up
- They prevent shocks from occurring when you are working near live electrical wires
- They also act as an anti-surge measure
Electrical safety standards and regulatory organizations
Today, several non-profit organizations invest their time and effort in developing and revising electrical safety standards. Electrical safety codes and standards drafted by these organizations reduce the loss of life and ensure the safety of property, electricians, and equipment.
Listed below are some organizations that help address the numerous concerns related to electrical power.
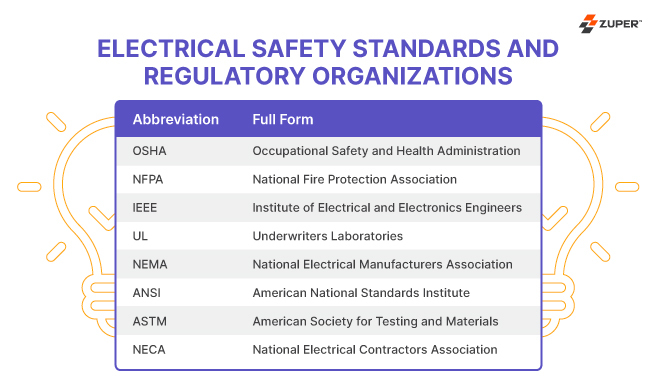
1. OSHA (Occupational Safety and Health Administration)
OSHA’s primary goal is to ensure a safe and healthy workplace for every American worker. They currently have 1000+ safety standards and regulations. Federal and state OSHA programs have several ways they can enforce regulations and workplace inspections are the primary way. They also offer voluntary assistance projects and training activities. If violations are found during inspections, OSHA levies penalties and citations.
2. NFPA (National Fire Protection Association)
The National Fire Protection Association (NFPA) has created standards designed to protect employees from the dangers associated with electrical power lines. The most well-known is NFPA 70E, which covers safety practices for working on energized equipment and establishing workers’ qualifications. It also offers guidance on establishing an electrical safety program in the workplace.
3. IEEE (Institute of Electrical and Electronics Engineers)
The Institute of Electrical and Electronics Engineers (IEEE) is a professional society that develops standards for everything from computer hardware to high-level programming languages. IEEE1584, entitled IEEE Guide for Performing Arc-Flash Hazard Calculations, provides methods for determining arc flash hazards from various sources. While other electrical codes are available in the industry to identify arc flash hazards, IEEE1584 has become the de facto standard.
4. UL (Underwriters Laboratories)
The Underwriters Laboratories (UL) is a nationally recognized testing laboratory. It is an independent testing organization that lists and labels products for conformance to accepted standards. Manufacturers routinely submit their products to UL for evaluation. UL awards a UL label to products that conform to preset electrical safety codes.
5. NEMA (National Electrical Manufacturers Association)
The National Electrical Manufacturers Association (NEMA) has over 400 member companies that manufacture electrical products. NEMA works hand-in-hand with the American National Standards Institute (ANSI) and the International Electrotechnical Commission (IEC) and takes on an advocacy role with UL and governmental agencies. ANSI has adopted several NEMA publications as American National Standards.
6. ANSI (American National Standards Institute)
The American National Standards Institute (ANSI) is a private, non-profit organization that administers the voluntary standardization system in the U.S. Working in conjunction with organizations such as NFPA, IEEE, NEMA, and ASTM, it publishes various industry consensus standards to be used by electrical workers around the world.
7. ASTM International (American Society for Testing and Materials)
The American Society for Testing and Materials (ASTM) has developed several electrical safety standards. Their standards primarily focus on testing and analyzing the quality of electrical products ranging from personal protective materials used by electricians to lubrication techniques.
8. NECA (National Electrical Contractors Association)
The National Electrical Contractors Association (NECA) develops installation standards for electrical construction projects. They place special emphasis on the safety of their members while developing electrical safety regulations. ANSI has started adopting these standards in many cases.
Conclusion
Electrical safety is one of the most important factors to consider when working around electrical equipment. It is especially true for electricians and service technicians because they have access to high-voltage systems that could cause serious injuries or deaths if not handled carefully.
By taking precautions and following safety guidelines, electricians can help reduce the risks they face on the job. By staying aware of potential hazards and being prepared for emergencies, electricians can keep themselves safe and help prevent life-threatening accidents.
If you are an electrical enthusiast, keep an eye out for our electrical blogs!